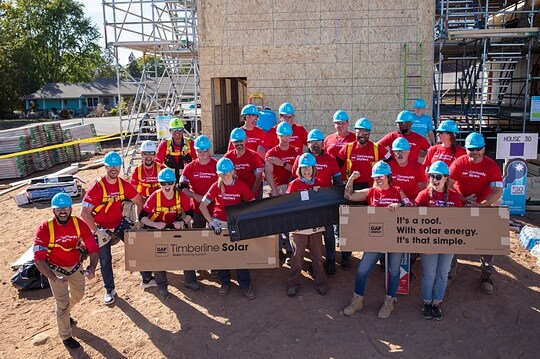
In Your Community
2024 Habitat for Humanity Carter Work Project in Twin Cites GAF Hometown
Under sunny blue skies, GAF hometown workers from Minneapolis joined over 4,000 Habitat for Humanity volunteers to donate their time and energy to the 2024 Carter Work Project in East St. Paul, Minnesota.The landmark 40th anniversary of the Carter Work Project celebrated former President Carter's 100th birthday. It also heralded the completion of 30 new all-electric homes in The Heights—the largest affordable housing development yet for Twin Cities Habitat—and marked the first installation of GAF Timberline Solar™ Energy Shingles.Supporting the Carter Work Project's PurposeGAF and the Habitat Carter Work Project share a common mission—to protect what matters most and bring people together to build homes, communities, and hope. Safe, secure, affordable housing is one of the surest routes to building resilient communities.Former President Jimmy Carter and former First Lady Rosalynn Carter were early champions of affordable housing. In 1984, they partnered with Habitat for Humanity to lead an annual week-long housing build. The momentum grew, and now, four decades later, over 100,000 Habitat volunteers have helped construct over 4,400 affordable homes for families in need.Each year, GAF volunteers travel from around the country for the Carter Work Project. GAF Community Matters also donates roofing materials, training, and installation expertise. Since 2011, GAF and its national network of certified contractors have supported roofing installation on over 3,800 roofing systems in collaboration with Habitat for Humanity, impacting more than 15,500 individuals.Building Resilience in MinnesotaThis year was particularly special thanks to first time solar shingle installation at a Carter Work Project. Even more, the project's location was in a GAF hometown and local GAF employees were on-site to volunteer.Benefitting Homeowners by Going Solar"We're donating 40 roofing systems and 40 solar energy systems from GAF and GAF Energy," says Jake Pream, a territory manager for GAF Energy in Minnesota.In addition to energy production, the beauty of the GAF Timberline Solar™ Energy Shingle is its simplicity. The nailable shingles are "just like your typical Timberline HDZ® Shingles," says Fan Ulacia, Director of Product Deployment Applications for GAF Energy and one of the minds behind the solar shingle design. "They're simple enough to install with a nail gun, but they produce energy." For Ulacia, improving access to solar energy, giving back to the community, and helping homeowners gain energy independence make GAF Energy a great fit for the GAF Habitat partnership."The solar-powered roofing system will make these homes more resilient, generate energy, and be a long-term benefit to Habitat homeowners by helping to offset their energy costs," adds Jeff Terry, vice president of corporate social responsibility and sustainability at GAF, who has volunteered at the Carter Work Project for 26 years.Helping a GAF HometownThe Twin Cities Habitat build is also special because it means the Carter Work Project takes place in a GAF hometown. As Pream, a St. Paul native, puts it, "I have friends and family quite literally a few houses down."The Minneapolis GAF manufacturing facility opened in 1935, and "it's something we're really proud of," says Austin Owens, a local GAF technical manager. Over the years, "we've made improvements to equipment and operations and made changes to help the environment and sustainability. We try to help the community as much as possible."Like many GAF volunteers at the Carter Work Project site, Joey Och, a GAF plant process engineer, grew up in the area. "Affordable housing is something Minneapolis and St. Paul have been pushing for," says Och, "so it's nice to be out here and help. Affordable housing brings more people into the community."With GAF donating roofing and solar energy systems for this year's project, safe and affordable homeownership, with reduced energy bills, will be accessible to more people.This housing security helps strengthen the community. The area may experience severe weather and its share of hardship, but "there's a lot of resiliency in this community," says Owens.Carrying On the Carter Work Project in 2024 and BeyondFor many reasons, the Carter Work Project inspires repeat volunteers. "Community does matter," says annual participant and GAF CARE Learning and Development Instructor Michael Humenik. "It's just fun to volunteer. I look forward to coming out every year."Habitat homeowners who return each year to volunteer are the true testament to the transformational power of access to safe, affordable housing. LeAndra Estes brought her hard work and a big smile to the week-long Twin Cities build. Estes is an annual volunteer for the program that changed her life. "I need and I want to give back to Habitat for Humanity, to the affiliates and partners, and to the future homeowners to come," she notes.Estes puts into words the value of affordable housing and how the benefits ripple far beyond the home. "When you have a home, you don't just have that home and your family. Your community also becomes your family," she explains.Although former President Carter has retired his tool belt after decades of humanitarian service, he surely must have been proud to see his legacy continue to evolve, especially with the revolutionary new solar shingle that supports homeowners' financial independence.Ready to get involved? Explore the Habitat for Humanity GAF Contractor Program and change lives for the better, starting today.
By Authors Annie Crawford
December 19, 2024