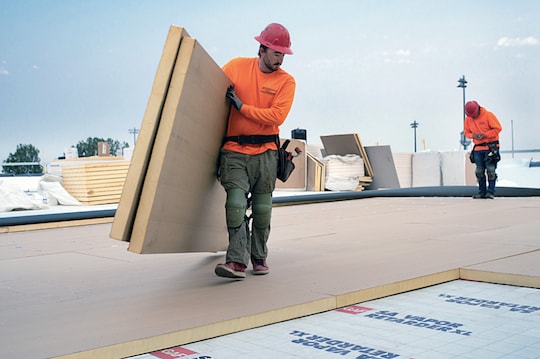
Part 1 of our discussion of parapets (Continuity of Control Layers) explored the many reasons continuity of water, air, thermal, and vapor control layers are necessary for long term performance.
In Part 2 of our discussion of parapets (Navigating Codes) discussed the challenges involved in navigating the range of national model codes and standards that will influence your design.
In Part 3, we're providing a practical example of applying the control layer continuity principles to construction trade sequencing while identifying some common challenges.
Control Layer Continuity
To better understand common parapet challenges, it is important to review continuity across the roof and wall systems, specifically the key four Control Layers: Water, Air, Thermal, and Vapor. These four key Control Layers should generally be continuous across all six sides of building enclosures. It is difficult–but not impossible–to achieve effective Control Layer continuity across building systems, especially at significant transitions like a parapet, where the roof system meets the wall system.
When beginning to think about designing enclosures, it's helpful to start with an ideal scenario. The configuration of the ideal wall system can be considered as follows: the cladding on the outside, continuous insulation keeping the rest of the control layers tempered in the middle, and structure to the inside. This "ideal" configuration can also be applied horizontally to the roof assembly. For an example of a transition, the roof and wall meet as an "ideal" flush edge with very simple transitions. As a system moves away from these ideal configurations, including parapets or other project constraints, transition details become more challenging and trade-offs have to be made.
"Ideal" Roof and Wall Transition
For more complex scenarios, like parapets, there are simple design tools to connect the control layers as they transition from the wall to the roof. The "pen test" — tracing each of the control layers across the building enclosure — is a helpful tool to design and communicate to the field the intent of the critical components and functions of the building enclosure.
Discussing control layers as they apply to a roof or wall alone is fairly manageable. But the process gets much more complicated when the roof meets the wall at the parapet condition (more here in Part 1 about Control Layers). The "pen test" is relatively easy in theory, but it can get complicated as we zoom in and consider the control layers at each condition, penetration, and transition.
Example of breaking down a parapet detail by the four control layers
In summary, the following are key points to maintain continuity of the control layers:
- Water Control is managed by the roof membrane and the cladding. A secondary water control layer is often found against the structure, behind or below the exterior insulation.
- Air Control can be managed at the deck level of the roof, which can more readily be married into the wall air barrier. The roof membrane can also be used as an air barrier as long as the detailing and transitions are done carefully.
- Thermal Control continuity is maintained by connecting the roof and wall insulation, which can be challenging. It's important to be mindful of cavity insulation and the potential design risks of condensation at the thermal bridges.
- Vapor Control can also be in the same plane as the air control layer, based on location needs, construction methodologies, and occupant use of the building.
Coordinating Complexity
This section provides a practical example of applying the control layer continuity principles to construction trade sequencing while identifying some common challenges. When confronted with a similar design as the example below, a general contractor may request alterations to the design in order to shorten the schedule or reduce costs. However, this value engineering process—the reduction of cost and time—may also comprise continuity of the control layers and reduce the intended long-term performance of the parapet systems (more about Value Engineering performance impacts). If unsure or designing high-performance buildings, engaging a building enclosure consultant can help anticipate continuity and constructability issues.
For the purposes of this discussion, the materials applied to the parapet assembly sequence (figures a – h below) are color-coded in their application step by their primary control layer function:
- Water Control elements are shown in "blue"
- Air Control elements are shown in "red"
- Thermal Control elements are shown in "yellow"
- Vapor Control elements are not shown separately (See the Vapor Control section above for applicability)
To help identify separate materials within a control layer, lighter and darker versions of the color are used to distinguish elements within the same step. Also dashed, or "hidden lines," are used to depict materials edges that may be overlapped or behind another layer in the sequence the same step.
(a) Initial condition
a. In the initial condition, the wall and roof deck are assembled up to their sheathing. The roof structure is a corrugated steel deck with a substrate board placed on top to provide a continuous surface for later air barrier adhesion. The exterior wall is steel framed with cavity insulation and exterior sheathing applied.
(b) Pre-treated corner
b: In preparation for the parapet wall construction, a strip of air barrier material is applied to the roof and wall edge with sufficient material for future integration with the remainder of the continuous air barrier. It is important to note the material on the wall side is not yet adhered to allow for future lapping to manage water in "shingle fashion" as required by the IBC. This can be accomplished by leaving a portion of the release liner in place for adhered materials.
(c) Parapet wall assembled
c: The parapet wall is then assembled on top of the roof deck in a platform framed configuration. If lateral bracing for the parapet is required, additional detailing and coordination would be needed.
(d) Air barrier integrated
d: After the parapet wall is in place, the remainder of the continuous air barrier can be applied to both the roof and wall systems. It is notable that if the air control layer is also intended to act as the WRB in the wall and parapet system (as shown in (d)), the application should start from the lowest point and work upward; this allows the subsequent layers to be lapped in shingle fashion. After the air barrier is applied to the walls (light red), the pre-applied strip of material can be lapped and secured over it (dark red in the center of the wall). The air barrier can then be applied to the roof deck (light red), up the backside and over the top of the parapet wall, and then terminate downward on the outside of the wall, lapping over in shingle fashion (dark red at the top of the wall). Lapped edges hidden behind the layers of air barrier materials are shown with dashed lines.
(e) Continuous insulation installed
e: The roof insulation and high-density coverboard can now be installed to the roof deck. These could be mechanically-fastened or adhered roof systems, but the use of mechanical-fasteners through the entire roof insulation can have a significant effect on the thermal performance of the building. Continuous insulation is also applied to the backside of the parapet wall to maintain continuity. The parapet blocking for the coping cap can now be installed. In this case, it also includes a layer of tapered insulation to provide slope back to the roof area and extend the continuous insulation to the top side of the parapet. Wood blocking is included as required to accomplish fastening to meet ANSI/SPRI ES-1 uplift requirements. After the parapet blocking is in place, a piece of counter flashing (shown in blue) is required to lap over the WRB prior to the installation of the walls continuous exterior insulation; flashing will later lap over the coping cap, but without this piece pre-installed, there would be a discontinuity in the water control layer. The bottom edge of the flashing, under the wall exterior insulation, is shown as a dashed line.
(f) Roofing and terminations installed
f: The roof membrane is applied to the roof area. An expansion joint may also be added at the joint between the roof and the parapet wall to allow for any expected movement between the systems. The membrane is then lapped and seams completed at the horizontal roof edge, extended up the backside of the parapet wall and terminated over the previously installed counter flashing on the face of the coping blocking. Terminating and lapping downward on the outside of the parapet wall maintains the continuity of the water control layer and provides a shingle-lap onto the secondary water control layer on the wall. The membrane over the coping blocking will also act as a secondary protection below the future coping cap. The coping cap attachment cleats and spline flashing are installed to the top edge of the parapet wall, bedding and treating the fasteners in sealant where they penetrate the membrane.
(g) Coping and cladding installed
g: The exterior cladding is then installed to the outside of the parapet and exterior walls (light blue). The coping cap is installed at the top of the wall, over the cleats and blocking (dark blue). The coping cap should be attached with the cleats as tested for by ASNI/SPRI ES-1, lapped over the cladding with drip edges on both sides, and maintain an overall slope towards the roof system to shed water.
Caption: (h) Final parapet assembly
h: The parapet assembly is now complete. During the service life of the building, regular inspections and maintenance are needed to retain the performance of the parapet. Recovering or replacement of the roof system in the future should utilize as-built documentation to understand how to continue to manage the wall and roof system control layers.
Enabling Success
Designing to maintain continuity of the four key control layers is important to ensure long-term performance. To get the design intent implemented in the field, detailing and identification of the control layer(s) in the drawings and specifications is critical. This can require the design to be pretty specific – more than just "or equal" or "by others". Specifying materials with known compatibility is important. And if the sequencing of components and members in the field impacts the intended continuity or performance of the control layer in the design – it should be addressed.
These challenges should be considered for every project. "Standard details" aren't able to capture project complexities such as high-to-low parapet transitions, terminations into a rising wall, and curtain wall flybys. These conditions all require unique detailing that must include continuous and well-conceived transitions. It's important to remember that control layer discontinuities can lead to failures in the field. For instance, air leakage can lead to concealed condensation, which can be mistaken for roof leaks.
For more information on parapet and control layer continuity, register for the Continuing Education Center webinar, Parapet Predicaments and Roof Edge Conundrums, sponsored by GAF and presented by Jennifer Keegan, AAIA and Benjamin Meyer, AIA, LEED AP.
For more information on parapet and control layer continuity, read the Continuing Education Center article, Parapets—Continuity of Control Layers, sponsored by GAF and written by Benjamin Meyer, AIA, LEED AP.