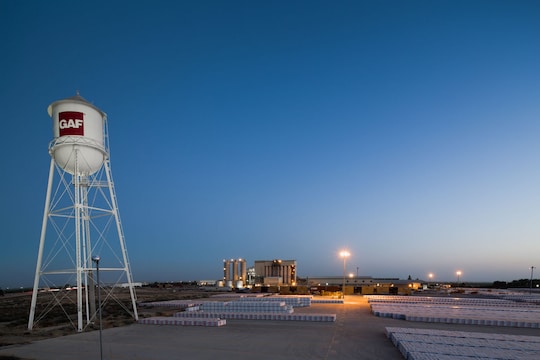
Manufacturing sustainability is a top priority for GAF. In 2022, the company announced its 2030 Planet Goals to "focus on operational improvements, product transparency, and the introduction of circularity in the asphaltic shingle industry."
Looking to lead positive change while considering the long-term impact of its business on the planet, GAF identified several goals, including:
Diverting 1 million tons of roofing materials from landfills while integrating recycled shingle materials into new shingle products
Diverting 80% of manufacturing waste from landfills, recycling all shingle and TPO scrap that results from the manufacturing process, and recycling or reusing fiberglass mat scraps and cores
Reducing embodied carbon and operation carbon throughout its manufacturing and operations
Achieving Environmental Product Declarations for its core products, conducting life cycle assessments, and generating 2.5 GW of power from solar roofs in partnership with GAF Energy
Meeting these goals takes time, resources, innovation, and ingenuity, all backed by a team working to build a better world. Every GAF location is striving to meet the company's goals. Looking back on the progress made in 2023, some impressive accomplishments are bringing the company closer to achieving full manufacturing sustainability.
Residential Manufacturing
The GAF Mt. Vernon, Indiana, shingle manufacturing plant worked toward achieving sustainable operations through robust recycling efforts. The team established a shingle recycling outlet estimated to divert thousands of tons of asphalt shingles from landfills annually. This has eliminated thousands of dollars in disposal fees and reduced transportation costs.
The Mt. Vernon staff found creative ways to keep complex waste materials out of landfills, including working with a local golf course that could take the plant's waste sand. The team implemented an internal recycling program that includes cardboard and packaging materials, increasing its waste diversion score.
Commercial Manufacturing
At the Gainesville, Texas, plant that manufactures TPO and Polyiso, team members earned the area's first waste diversion certification for both products' waste streams. They also earned a recycled content certification for each.
The plant established a trial program with a plastics recycler to reprocess TPO skin material for reuse in manufacturing new material. Recycling and reusing would divert thousands of tons of waste from landfills and use recycled materials in manufacturing flexible TPO for flashings.
The plant also developed a program with a local recycling company that serves as a single source to take its pallets, large cardboard boxes, facers, paper, and plastics.
Sustainability All-Stars
Recycling and manufacturing sustainability programs wouldn't be possible without the people behind the initiatives. GAF is proud to spotlight these individuals who went above and beyond to meet the company's sustainability goals.
Ben Anselman
As part of the Mt. Vernon team, Anselman was critical to starting the plant's core recycling program. He initiated repairs to an existing baler and established a program for recycling the super sacks. His creativity sparked the partnership with the local golf course to divert aggregate waste from landfills. In addition, he was the champion for the shingle recycling outlet project and repurposed an existing compactor to reinstate a cardboard recycling initiative.
Christina Talladira and Amy Wilson
These teammates lead the core recycling program at the Tampa, Florida, manufacturing plant. They worked together to establish aggregate and shingle recycling programs with their local recycling company. Talladira and Wilson consistently look for ways to divert waste streams from landfills. They also handle the administrative needs accompanying these programs, including scheduling loads and tracking waste.
Jeremy Tisdale
At the Tuscaloosa, Alabama, plant, Tisdale took the initiative to improve its core recycling program and set up a cardboard recycling program. He also championed a baler trial for glass mat cover and core waste, developing standard operating procedures and a job safety analysis. He was the innovator behind diverting the plant's plastic waste from landfills. He created a program where stretch film and shingle bundle packaging waste is saved in Gaylord boxes and then baled whenever the plant has downtime.
Pete Weyrens
In Gainesville, Texas, Weyrens is the champion behind the plant's recycling efforts, establishing relationships with the local recycling company. He also organized the flexible TPO skin material trials. This effort will divert thousands of tons of waste from landfills and use recycled materials to manufacture flexible TPO for flashings.
Leslie Peels
After the plant in Cumming, Georgia, saw a drop in its year-over-year waste diversion rate, Peels stepped in to turn those numbers around. Leading the effort to separate recyclable materials from regular waste, the Cumming location saw an impressive increase in keeping waste out of the landfill. Peels also set an example in data collection and analysis to keep the plant's sustainability goals on track.
TJ Jenkins and Todd Winstead
Jenkins and Winstead represent the TPO team at the Mt. Vernon manufacturing plant. Working together, they used their knowledge and experience in the TPO manufacturing process to help earn the plant's recycled content certifications. They also found a way to divert calcium chloride from local landfills and continue to work closely with the sustainability team to support waste diversion efforts.
Sustainability Promise
GAF is committed to "Protect What Matters Most," and that includes people, communities, and the planet. Its sustainability promise is an opportunity to invest in a healthy future for everyone. Learn more about that commitment in its sustainability report.